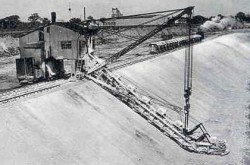
Die alten Römer gelten als Erfinder des Zements (caementum). Die heutige Art Zement zu produzieren, geht auf den Engländer John Aspdin (*1778-1855†) zurück. Er entwickelte 1824 ein Verfahren, um einen hoch druckfesten Baustoff herzustellen, der auch ohne Luft aushärten kann. Da das Produkt dem grauen Kalkstein an der englischen Küste bei Portland ähnelte, nannte Aspdin es „Portlandcement“. An seinem Grundrezept hat sich bis heute wenig geändert. Kalk (vier Teile), Ton (ein Teil) werden bei bis zu 1.400 Grad „gesintert“ und dadurch zu „Klinkern“ gebrannt. Die Klinker werden fein zermahlen und Gips (5 Prozent) zugemischt, um die Zeit des Aushärtens zu verlängern. Das neue Bindemittel, das gemischt mit Sand und Steinen (dem „Zuschlag“) als „Beton“ verbaut werden konnte, breitete sich rasch aus. In den 1840er Jahre stellten bereits zwei Kalkbrennereien in Kiel Zement in kleinen Mengen her. 1842 kam eine weitere Produktionstätte in Uetersen dazu, 1859 entstand eine Fabrik in Pahlhude an der Eider in Dithmarschen (bis 1901). Sie bezog den Grundstoff Kalk aus dem Ausland. In dieser Zeit entstanden auch in Flensburg (bis in 1880er Jahre) und Brunsbüttel (bis 1916) Fabriken. Alle mussten die Rohstoffe über weite Strecken beziehen. 1862 schließlich überzeugte William Aspdin (*1815-1864†), der Sohn des Portlandcementerfinders, den Iren Edward Fewer, die Produktion von Zement in Lägerdorf bei Itzehoe aufzunehmen. Damit war die erste Fabrik in den Herzogtümern direkt auf der Kreide, dem porösen Kalk, als wichtigstem Rohstoff der Zementindustrie entstanden.
Ein Ire als Pionier
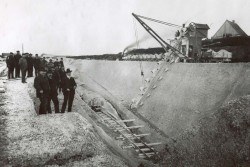
Südöstlich von Itzehoe hat der Salzhorst von Krempe eine bis zu 400 Meter mächtige Kreideplatte aus der Tiefe bis dicht unter die Erdoberfläche gedrückt (siehe Eiszeitland). 140 bis 60 Millionen Jahre vor unserer Zeit hatte sie sich damals in den Tiefen des Meeren aus den Kalkschalen abgestorbener Tiere gebildet. Besonders die jüngsten Schichten, die „Schreibkreide“, sind erdgeschichtlich interessant. Nirgendwo anders in Mitteleuropa sind die dramatischen letzten Abschnitte der Kreidezeit, in der drei Viertel der damaligen Lebewesen – vom Saurier bis zum Ammoniten – ausstarben, so vollständig dokumentiert wie bei Itzehoe. An keiner anderen Stelle in Norddeutschland sind die Kreidevorkommen jedoch auch so reichlich und derart leicht abbaubar. Um Itzehoe war so seit 1737 Kreide gegraben worden. Schlemmkalk, Dünger und Kreide sowie Mörtel wurde in Klein- und Kleinstbetrieben hergestellt. Der wilde Abbau der „Witteer“ (Weißerde) führte zum Streit zwischen den Bewohnen und den Grafen zu Rantzau als Grundbesitzer. 1828 wurde die erste Kalkfabrik gegründet. Bis zum Anbruch der Portlandzeit 1862 stieg die Produktion insgesamt auf knapp 1.000 Tonnen an.
Drehöfen verändern alles
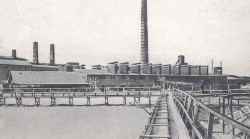
Die Portlandcementfabrik von Fewer war die erste am Ort. 1863 folgte an der Stör die Alsensche Fabrik, 1876 dann das Werk „Holstein“, 1884 schließlich die Breitenburgische Portlandcementfarbrik. Alsen (APCF) und Breitenburg (BPCF) erwiesen sich bald als die leistungsfähigsten Betriebe. 1889 schon übernahm Alsen das Werk von Fewer, 1905 Breitenburg das Werk Holstein. Der Konzentrationsprozess endete 1972 mit der Fusion zu den „Alsen-Breitenburg Zement- und Kalkwerken“. Zehn Jahre später wurde die Produktion auf dem Alsengelände an der Stör in Itzehoe eingestellt. Nach über 120 Jahren war damit auch klar, dass ein Zementwerk am günstigsten „auf der Kreide“ steht. Um Zement nach Hamburg verschiffen zu können und von dort Kohle zu holen, war Alsen nach Itzehoe an die Stör gezogen. Dafür wurde die Kreide seit 1868 auf der Schiene zum Werk gefahren. Zuerst zogen Pferde die Loren, von 1877 an Lokomotiven. Um die Jahrhundertwende produzierte Alsen mit 600 Mitarbeitern schon über 100.000 Tonnen Zement pro Jahr und modernisierte weiter. 1908 baute Alsen eine zwölf Kilometer lange Drahtseilbahn über die Stadt, die den Ton aus der Region um Wacken zum Werk brachte. Sie blieb bis 1974 in Betrieb. Drahtseilbahnen zum Transport der Kreide nutzte auch Breitenburg bis in die 1960er Jahre. Der Weg von der Breitenburger Fabrik zum Wasser war durch einen bereits 1878 erbauten Kanal zur Stör gesichert. Ab 1907 ersetzten die Fabriken die traditionellen Schacht- durch Drehöfen, die nun eine kontinuierliche Produktion zuließen. In die leicht abschüssigen Drehzylinder wird am hohen Ende Kreide-Ton-Schlamm eingebracht. Er bewegt sich im drehenden Ofen auf die Feuerung am unteren Ende zu und wird dort zu Klinkern gesintert. Nach dem sogenannten Gegenstromprinzip arbeiten heute alle Zementöfen.
Zement für Stahlbeton
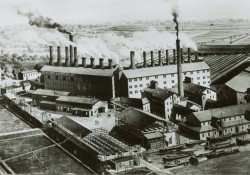
Erst nachdem man gelernt hatte, Beton mit Eisen zu „armieren“, wurde er zu einem universellen konstruktiven Baustoff. Schon Mitte des 19.Jahrhunderts waren in Frankreich erste, kleinere Objekte so verstärkt worden. Einer der Pioniere war der Gärtner Monier. An ihn erinnern bis heute die „Moniereisen“. Doch erst um 1870 setzte sich der Stahlbeton für den Bau durch. In der Gründerzeit konnte die Produktion deshalb stetig gesteigert werden. Besonders von Breitenburg aus wurde Ende des 19. Jahrhunderts viel Zement in die deutschen Kolonien verschifft. Die Arbeiter antworteten deshalb auf die Frage, wo sie arbeiteten: „auf Kamerun“. Über 3.000 Menschen arbeiteten in den Hochzeiten in den Kreide- und Tongruben, an den Öfen, den Mühlen und den Ladepiers. Ihre Zahl ist durch die Konzentration und die Mechanisierung heute auf unter 500 gesunken. Das spiegelt auch die Geschichte von Lägerdorf, das bis 1860 noch ein Bauerndorf war. In den Hochzeiten der Zementkonjunktur vor dem Ersten und nach dem Zweiten Weltkrieg wuchs es auf weit über 4.000 Einwohner an. Inzwischen ist die Zahl auf 2.660 (2020) gesunken, die wenigsten arbeiten noch „auf Breitenburg“.
Kreide satt
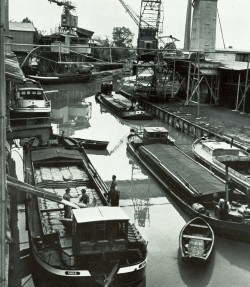
Die einzige Sorge, die es für die Zementindustrie um Itzehoe nie gab, war die um den wichtigsten Rohstoff, der Kreide. 1994 wurden allein für die genehmigten und beantragten Abbauflächen die verfügbare Menge auf 163 Millionen Tonnen geschätzt. Nachdem die Bahn, und die Pipeline (Alsen von 1966 bis zur Fusion) durch Förderbänder abgelöst wurde, können darüber noch für Generationen Kreide in die Fabrik transportiert werden. Seine höchste Produktivität erreichten die Portlandcementwerke nach dem Zweiten Weltkrieg. Die Phase begann durch Exporte und ging nahtlos über in die Aufbauphase der Bundesrepublik. 1969 wurden erstmals über eine Millionen Tonnen hergestellt. Da reichlich Kreide und – wenn auch immer weiter entfernt – Ton vorhanden war, wurden Transport und Energiekosten – also Strom für die Maschinen und Brennstoff für die Öfen – immer bedeutender für die Kalkulation. Um sieben Tonnen Zement zu brennen, braucht man eine Tonne Kohle. Ende der 1960er Jahre wurde die Kohle durch das preiswertere ÖL ersetzt.
Intelligente Produktion
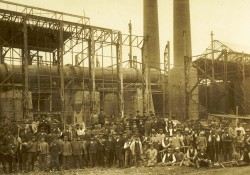
Nach den Ölkrisen kehrte man zur Kohle zurück. Sie wird heute als Staub verbrannt. Mitte der 1970er Jahre war mit einer Jahresproduktion von über zwei Millionen Tonnen der Zenit überschritten. Alsen Breitenburg war seit den 1960er Jahren mit dem Schweizer Zementkonzerns Holderbank AG verbunden. 2003 ändert sich deshalb der Name. Aus der Alsen AG wurde Holcim. Der Zementhersteller versucht heute im Wettbewerb auch dadurch zu bestehen, dass man die Anlagen intelligent nutzt. Das gelingt vor allem durch Kreislaufprozesse und dadurch, dass es möglich ist, problematische Abfälle als hochwertige Rohstoffe einzusetzen. So geht Kreide aus Lägerdorf in die Rauchgasentschwefelungsanlagen der Kohlekraftwerke.
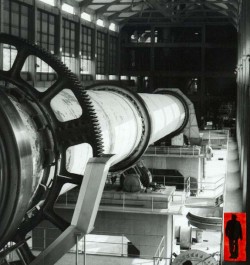
Die Kreide entzieht dem Rauch die Schwefelsäure und wird dadurch zu Gips, der im Zementwerk den Naturgips ersetzt. Statt Ton wird seit über zehn Jahren die chemisch fast identische Flugasche eingesetzt. In den Drehöfen wird inzwischen auch hochbelastetes Altöl und – in der BSE-Krise – auch Tiermehl verbrannt. Die hohen Temperaturen und die lange Verweildauer in den riesigen Brennkammer garantieren, dass alle gefährlichen Stoffe vernichtet werden.
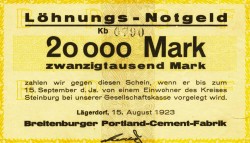
Werner Junge (0302/0721)
Quellen: Sönke Nagel, Die Zementindustrie im Raum Itzehoe, Flensburg, 1988, Heft 13, Flensburger Arbeitspapiere zur Landeskunde und Raumordnung, ISSN 0932 – 9404; Minister für Wirtschaft,Technik und Verkehr des Landes Schleswig-Holstein (Hrsg.), Rohstoffe in Schleswig-Holstein, 1994; Alsen’sche Portland-Cement-Fabriken KG (Hrsg.), 1863 – 1963 / 100 Jahre Alsen, 1963, Hamburg;Heinz-Otto Lamprecht, Opus caementitium: Bautechnik der Römer, 1987, Düsseldorf, Beton-Verlag, ISBN 3-7640-0229-8; Klaus-Joachim Lorenzen-Schmidt und Ortwin Pelc (Herausgeber), Schleswig-Holstein Lexikon, 2. erweiterte und verbesserte Auflage, 2006, Neumünster, Wachholtz-Verlag, ISBN 13: 9-783529-02441-2
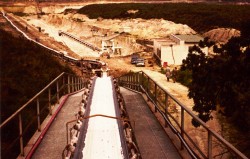
Bildquellen: Alsen-Breitenburg Zement- und Kalkwerke, Festschrift 100 Jahre Alsen, Gemeinsames Archiv der Stadt Itzehoe und des Kreises Steinburg